By Webb Girard and Dave Lundahl
Once a final prototype gold standard has been developed, the next sprint in the CRAEVS solution is to rapidly scale up the processing of the prototype into a commercially produced product. This sprint involves Benchtop Development followed by Pilot Testing and Plant Trials. Benchtop development typically starts with a technical review exploring the components needed to successfully scale the prototype into a product; ingredients, shelf life, packaging, financial modeling, processing, and regulatory considerations. This review is then used to build a benchtop scaling model of the commercialization process through a design of experimentation (DOE). The DOE is critical to a successful scaleup as it considers the initial formulation, ingredient functionality, and how best to mimic product processes on the bench. If Benchtop Development is done in a vacuum (i.e. without a DOE), successful translation to full production will be difficult and may result in significant redesign.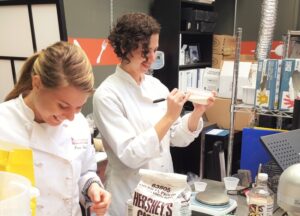
Benchtop Development also involves the use of industrially sourced, rather than commodity ingredients. While commodity ingredients can be purchased at retail, they often carry unwanted functionality, shelf life extenders, or other undesirable additions that can impact the final product. Specialty industrial ingredients can also perform differently in the formulation and cannot be assumed to be a one for one swap. Due diligence in establishing ingredient parameters will assist in the consistency of flavor and function through the formulation. Pilot Testing applies the Benchtop development scaleup model based on DOE to yield minimum batch size production runs that will prove the formula out in a scaled environment. Moving from 500g benchtop batches to 500lb production batches is not always seamless. The goal of this testing is to determine where the breakpoints are with minimal risk and maximum gain. This can involve formula adjustments (moisture, viscosity, functionality) to align with processing specifications or an equipment adjustment (speed, temperature, time) to produce the desired end product. It can also lead to larger formula modifications or equipment adjustments that need to take place prior to Plant Trials.
If there is a time to learn through failure, this is the optimal opportunity to do so. During Pilot Testing, data and parameters are measured and recording for building processing specifications and confirmation of final product attributes. In preparation for Pilot Testing, when possible, two to three times the amount of materials should be procured to account for the unexpected. Depending on the process, there may be time to run a few iterations per product and maximize learning. Initial production samples can be used to begin shelf life studies to begin to understand the impact of scaling and packing on the long-term quality of the product.
Plant Trials involve full batch size production testing. Modifications from Pilot Testing should be put into place prior to Plant Trials, either formulation or equipment. With Plant Trials the goal is to run the line at full capacity and ensure adjustments from the Pilot Test is carried forward and is scalable. By increasing the size of the batches, there is more product and processing time to make observations and adjustments on batching, cook cycles, and other processing steps can be made. Where Pilot Testing may only allow and hours or two of continual production, Plant Trials gives more line time and opportunities to for refinement on process and quality controls. By the end of Plant Trials, the product should be ready for full scale, all day production.